Christchurch Wastewater Treatment Plant Step Screens
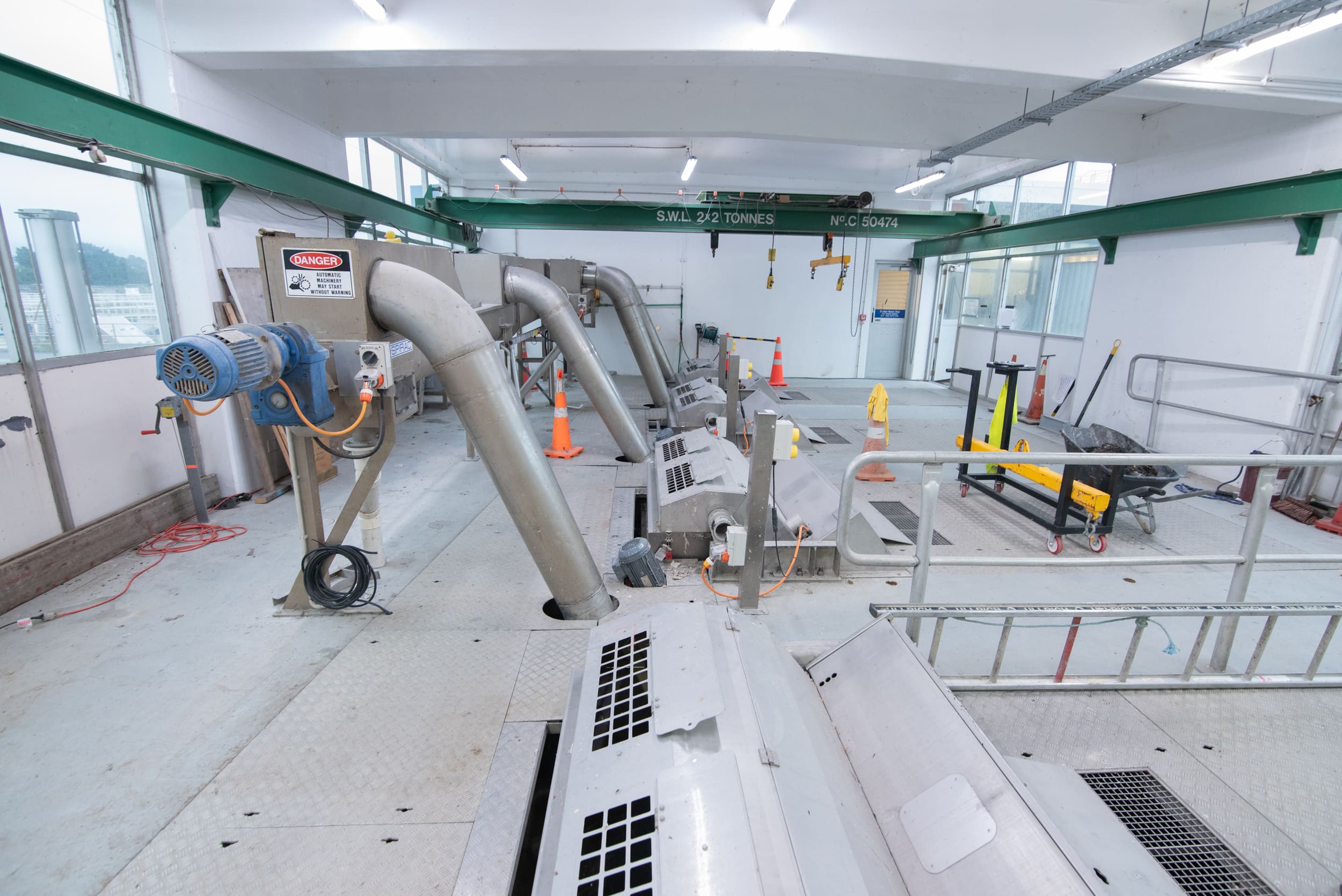
Seipp Construction worked with Christchurch City Council to supply and install new step screens and wash presses at its wastewater treatment plant, improving filtration efficiency.
Operating as the main contractor, Seipp Construction supplied, installed, commissioned and handed over four step screens and wash presses at the Christchurch Wastewater Treatment Plant. The new screens replaced the existing step screens, which were installed in 1997 and were nearing the end of their serviceable lifespan.
The step screens treat sewage waste as it first enters the treatment plant. Immersed at an angle in concrete-lined channels, they mechanically lift insoluble material out of the flow of wastewater.
‘In replacing the screens, we have been engaged in screen procurement and installation, and all the associated mechanical, electrical and civil work,’ explains Seipp Project Engineer Fiona Gillani. ‘Given our experience with pump stations, Christchurch City Council trusts us to manage multi-disciplinary teams to deliver on time and on or under budget.’
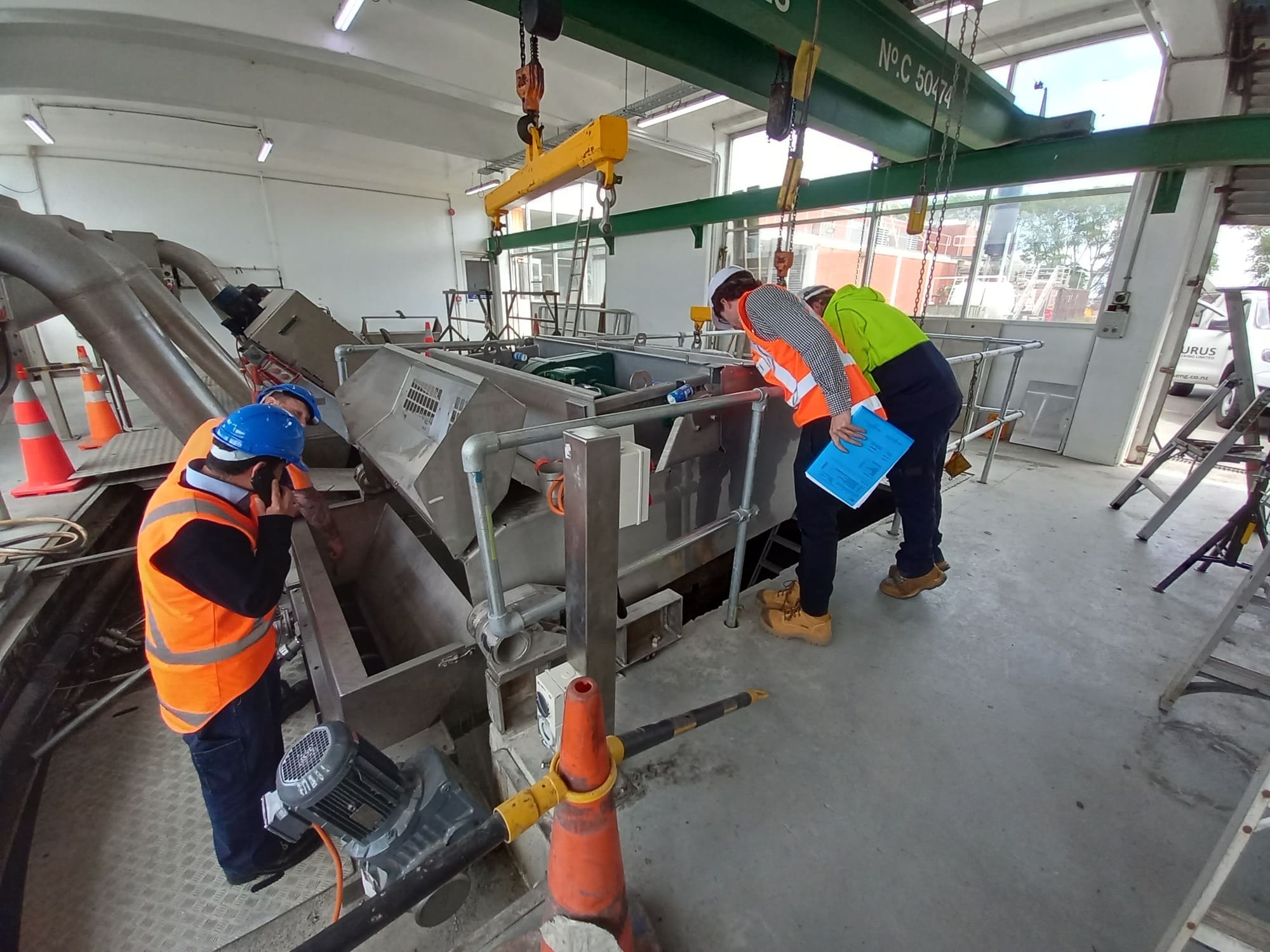
Lifting solids efficiently from wastewater
Each step screen comprises multiple racks of lamellae – thin metal plates – separated by 3mm plastic spacers. The first rotating rack of lamellae, located at the bottom of the screen, lifts solids – known as ‘rag’ – out of the wastewater and onto a rack of fixed lamellae, from where the next rotating set lifts the waste to the next fixed set, and so on, in a series of ‘waves’.
At the top of each screen, rags pass via a hopper into a wash press unit housing a horizontally oriented auger, where they are conveyed, washed, dewatered and compacted before being pushed via a main conveyor into skips and, finally, landfill. Step screens are self-cleaning when well-maintained, with regular checks and removal of stone and grit to keep the lamellae clear.
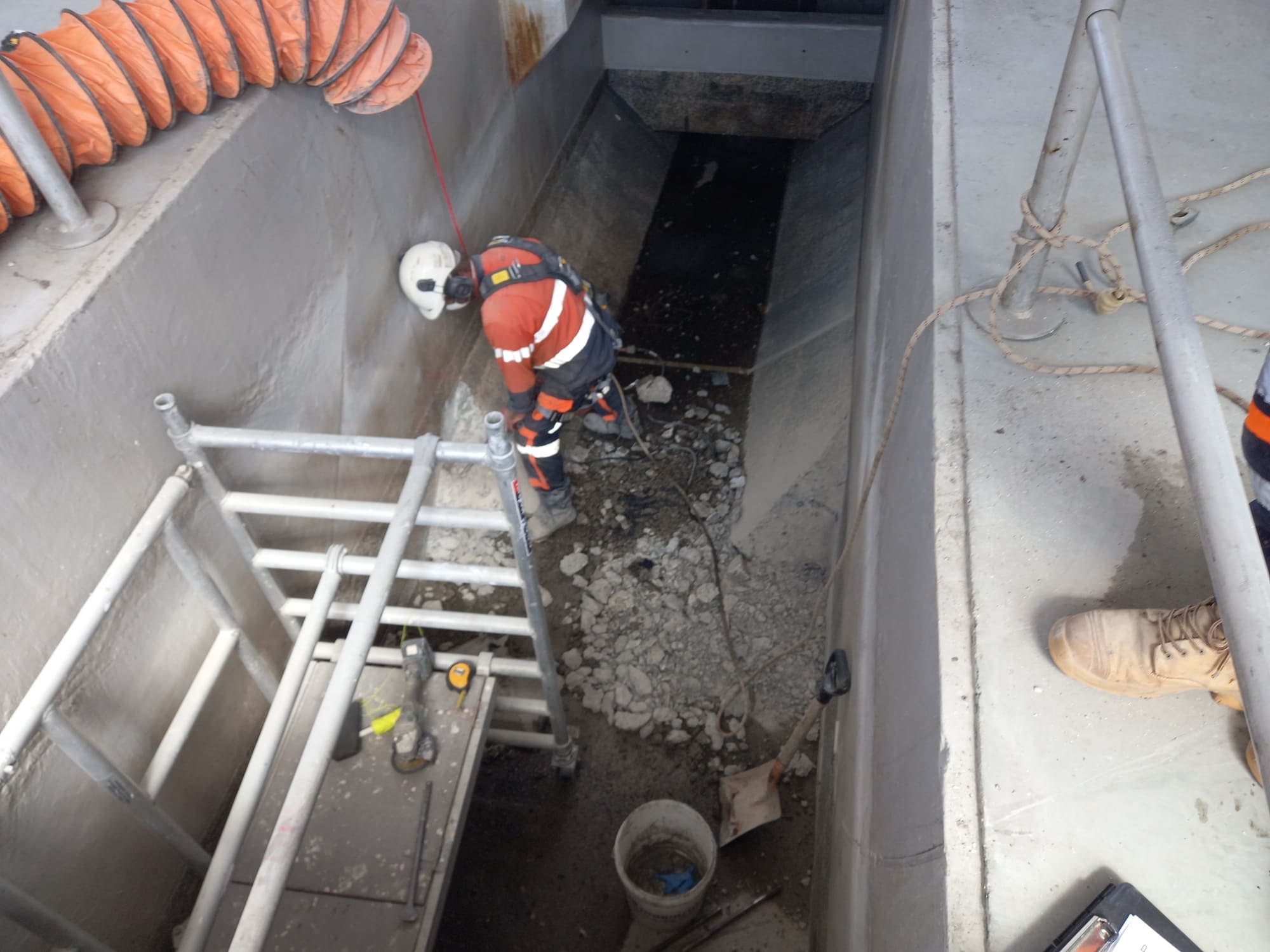
Staged work keeps screens running
‘As the city’s main treatment plant, the filtering process had to remain operational throughout the replacement programme,’ says Fiona. ‘We worked on one screen at a time, allowing two weeks isolation for each, to minimise disruption.’
Seipp worked closely with the structural engineer on the design of a new pair of transfer beams for each screen’s pivot brackets. ‘Getting these beams custom-built enabled us to reuse existing anchor bolts in the concrete,’ says Fiona.
Once the first replacement screen was installed, tested and commissioned, we ran the screen for an eight-week trial period. We checked that everything was running smoothly, at the correct (or better) rag extraction rate and quality as indicated in the manufacturer’s performance data.
‘There were no surprises: everything performed very well overall, and maintenance (which involved targeted checks for wear or damage, cleaning of components, repair or replacement of any parts as necessary) was much quicker – less than a day of cleaning per screen compared to the old screens, which could take several days each to check and clean,’ says Fiona.
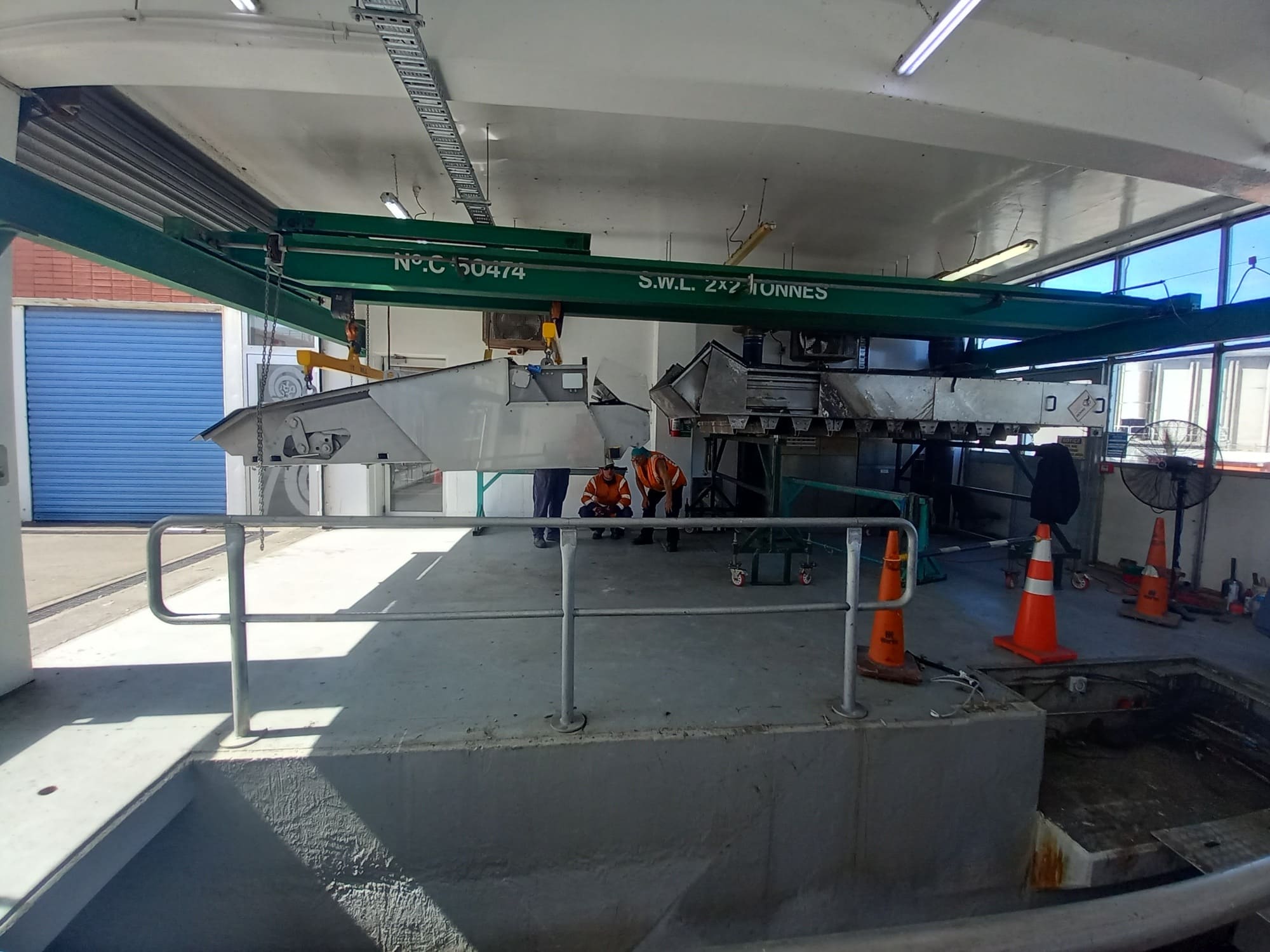
Close liaison with council upholds safety and efficiency
Throughout the work, Seipp remained fully committed to the council’s extensive safety procedures and hazard register. With council operators and tradespeople frequently on site, there was close liaison between Seipp and council on-site employees.
‘We were running a site within a site, and maintained Seipp standards in our work throughout. We regularly notified council’s operation and maintenance teams about our ‘3 Week Look Ahead Programme’ and our daily ‘Plan for the Day’, so that they knew in advance exactly what we were doing,’ notes Fiona.
‘We obtained Council Permits to Work under which we issued our own permits for Confined Space Working, and we had face-to-face talks with their screen room maintenance team. We would adapt to each other’s needs, which worked well throughout the installation and testing period, and we were efficient: overall we were in and out within 270 days.’
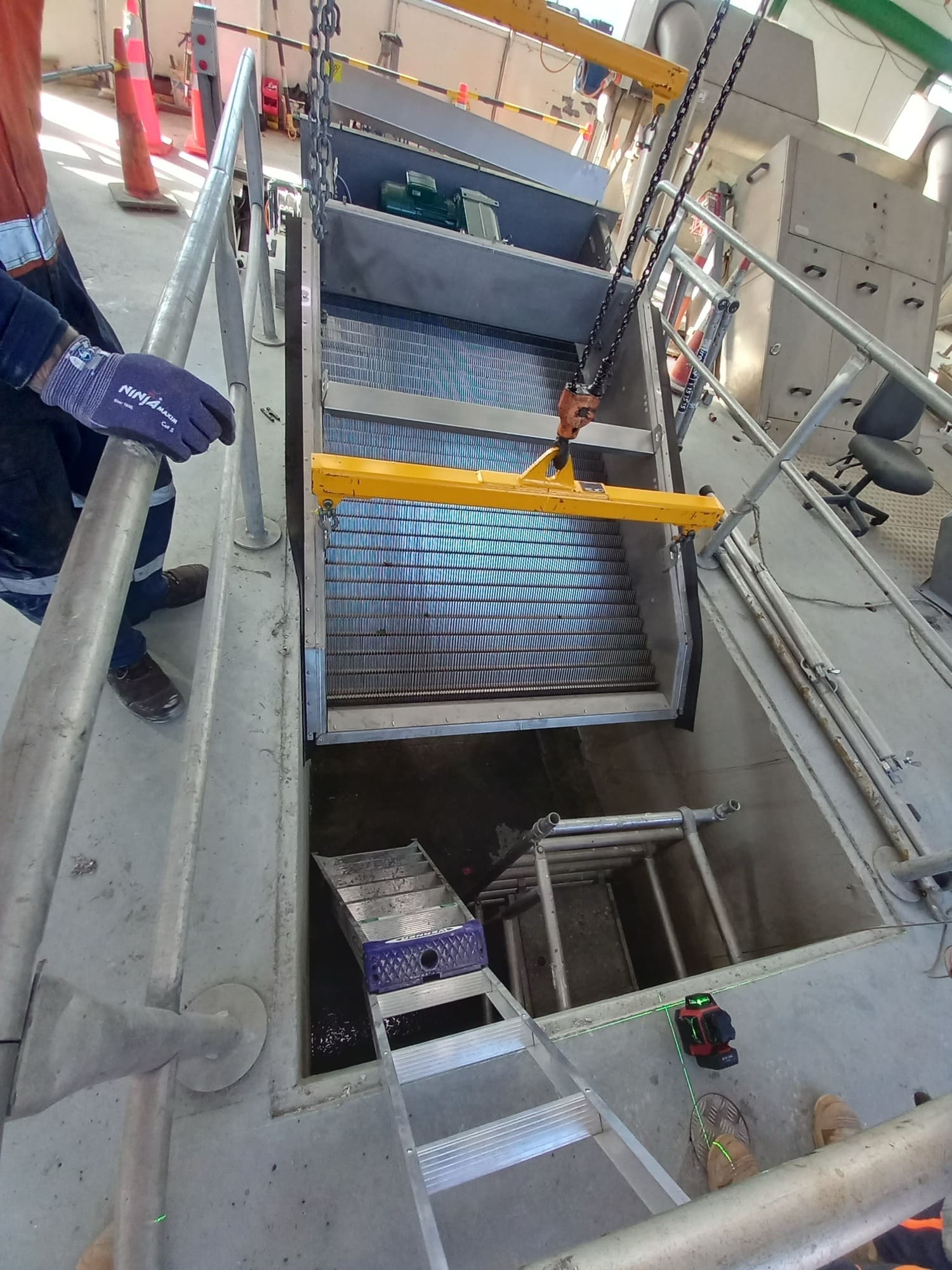