Benmore Dam Hydro Station Seismic Strengthening
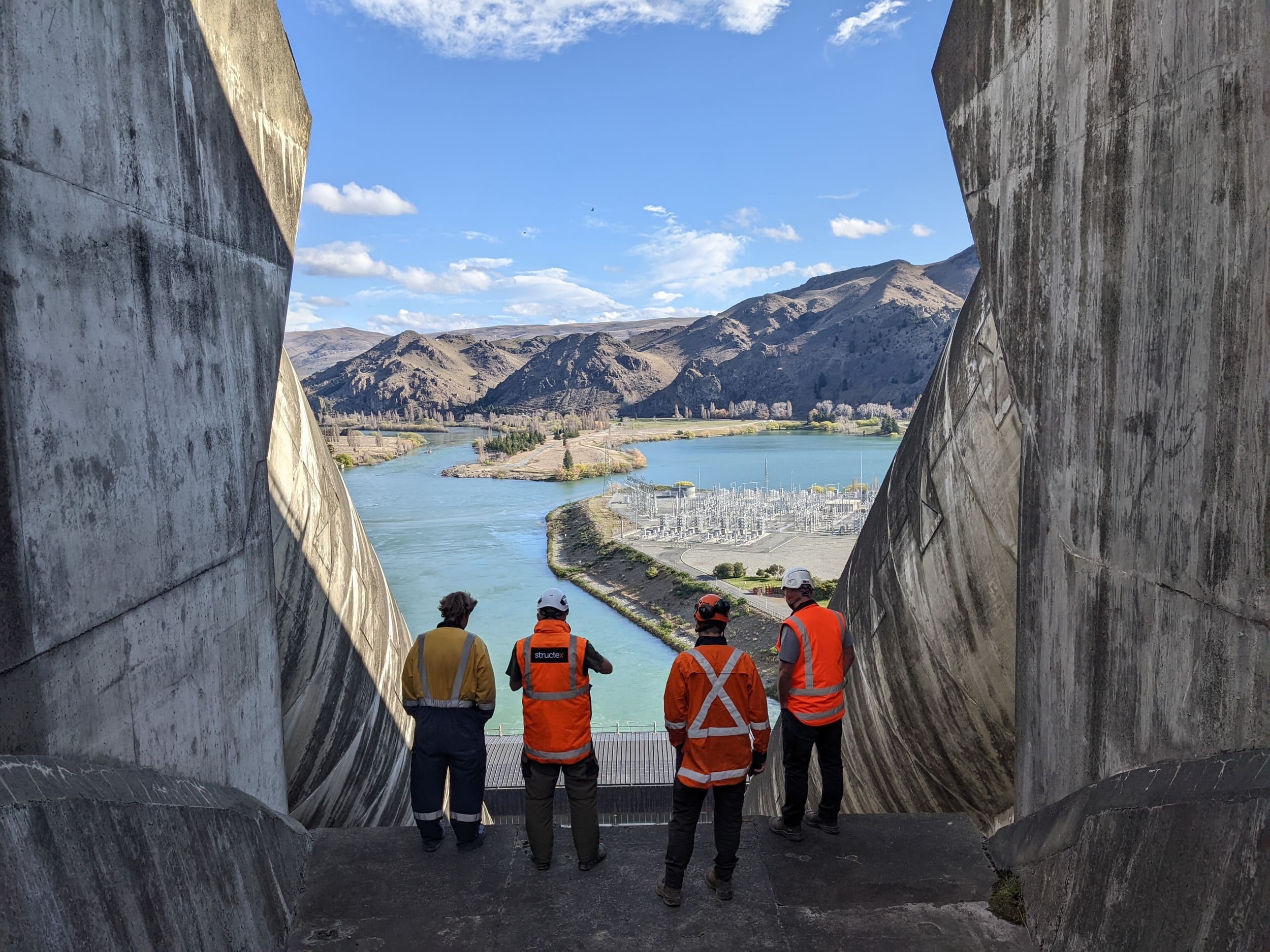
Seipp Construction implemented bespoke processes for bearing replacements and other upgrades to the penstocks on Benmore Dam.
In 2023, Seipp Construction worked with designer Structex on upgrading the penstocks at the Benmore Dam to meet current seismic resilience criteria. The Benmore Dam is the second-largest hydro facility in New Zealand, and Meridian Energy’s second-largest asset. Generating over 540 megawatts of electricity, it is a nationally critical piece of infrastructure. We were engaged at an early contractor involvement phase in order to add value to a project estimated at $65 million.
The project was split into three parts: replacing all 636 elastomeric bearings beneath the penstocks, installing 24 fluid viscous dampers midslope, and constructing 12 reinforced concrete sleeves around the existing anchor blocks. The prestressed concrete penstocks, which carry water from the lake to the turbines, measure 120 metres long and 5.2 metres in diameter. Built on a 37-degree slope, they presented a significant fall hazard and created a unique challenge for design, methodology and safety.
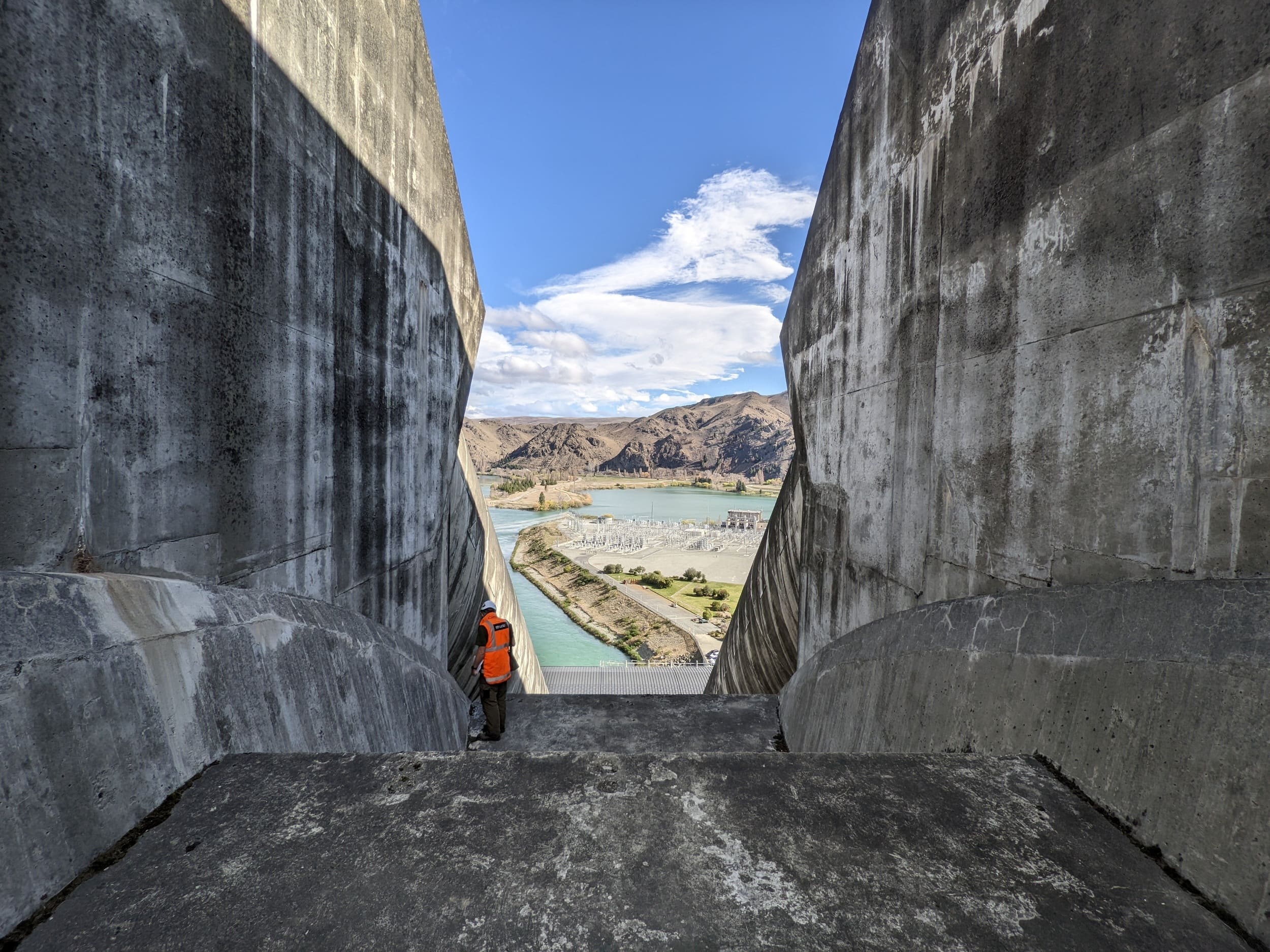
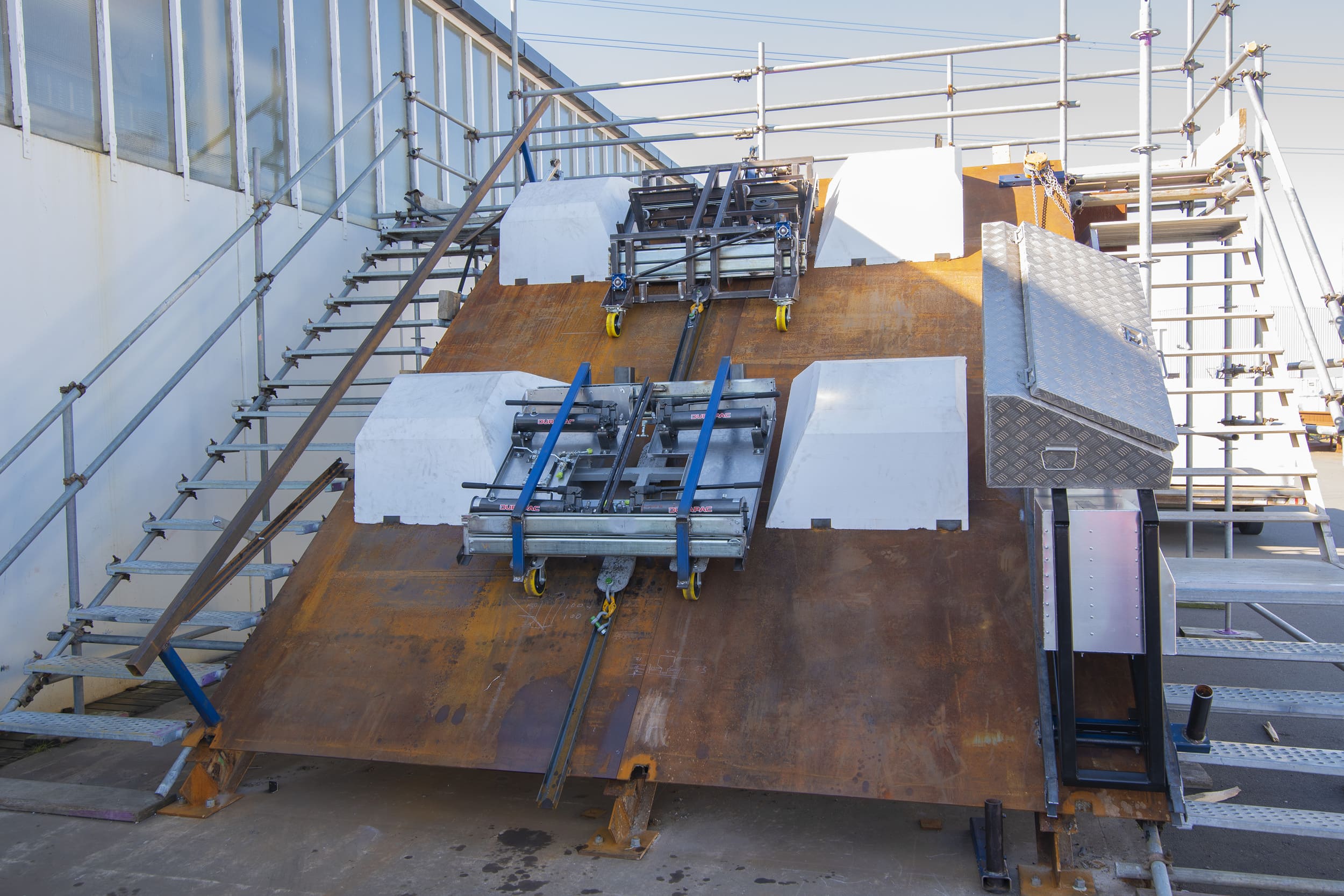
Tailored solution for replacing bearings on active penstocks
As the bearing replacement was the first of its kind in New Zealand, we co-designed a range of bespoke equipment for the specific geometry and the challenge of removing the bearings under significant compression from each 5000-tonne penstock above. (The penstocks had to remain in service throughout the project’s duration, and since the original tender had called for full penstock shutdowns, our new methodology was a major success.)
We collaborated with specialist subcontractor Taurus Engineering to design and trial a winch-and-trolley system that would enable equipment to be mechanically moved up and down the steep slope. The trolley hoisted the hydraulic jacks that would locally support each penstock while its elastomeric bearings were replaced.
This was a huge geometrical challenge on account of the small gap beneath the penstock and between the bearing plinths. The trolleys had to be winched up the slope, manoeuvred into a restricted stowed position, then extended outwards with millimetric precision to align with the replacement bearings. Given that the hydraulics and electronics themselves weighed over a tonne and would be cantilevered out at a steep angle, we first trialed the mechanical systems on a slope mock-up in Christchurch before heading to trials on a live penstock at Benmore. This solution would shorten the construction programme by two years and save Meridian $65 million in electricity generation costs.
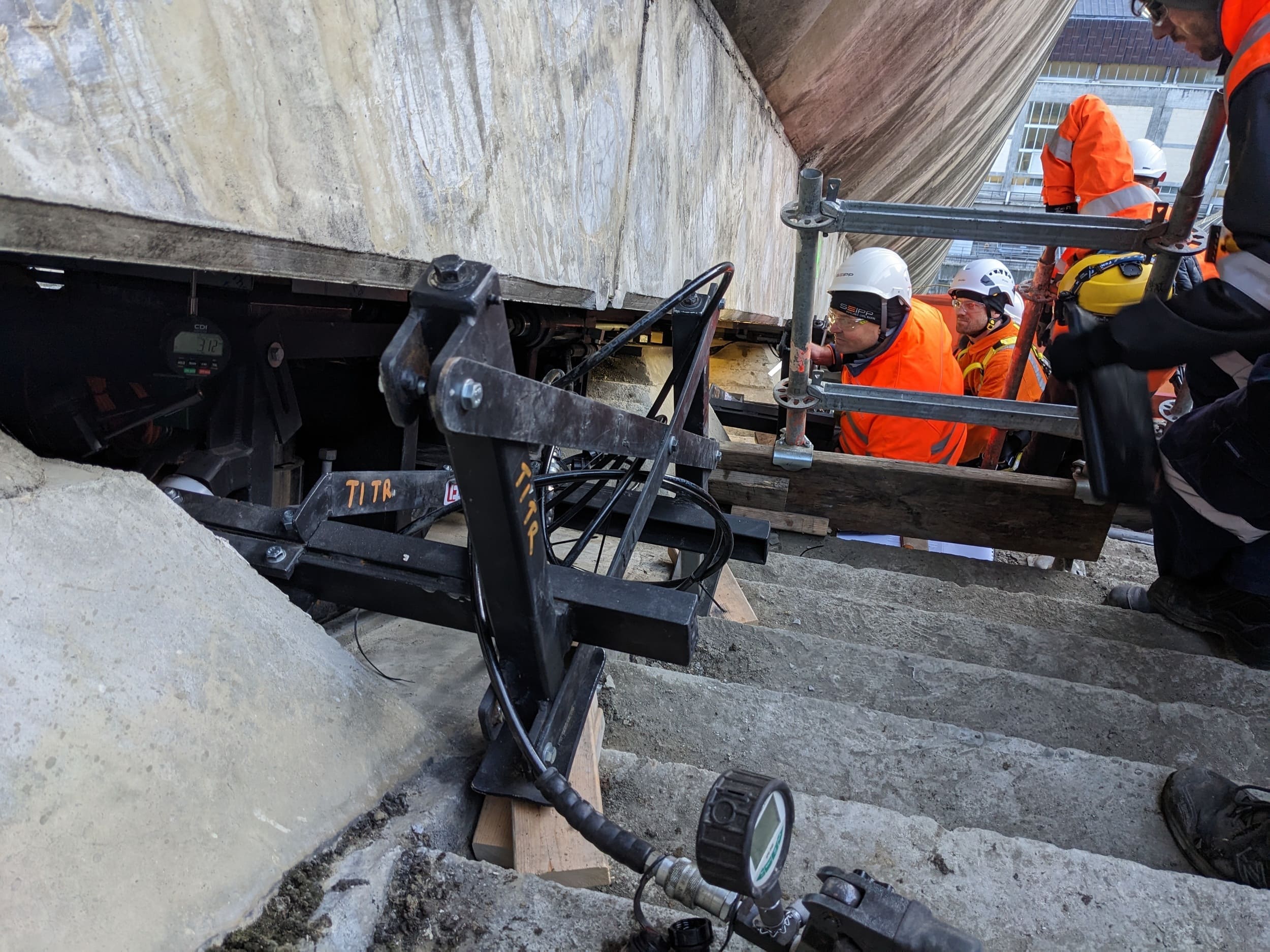
Preplanning fluid viscous damper installation
Meanwhile, we worked with Structex to develop a logical and constructable design for the fluid viscous dampers. This design development added value to the client: first by identifying early on the high cost of rock anchor installations, and next by mitigating this cost through design of an alternative raft foundation arrangement.
The fluid viscous damper installation involved a complex launch of 48 12-metre structural beams beneath the penstock to accurately connect into pre-installed brackets. With the added challenge of the slope, this launch required detailed sequencing, so a temporary frame-and-roller system was used to launch the beams accurately. We detailed the bespoke lifting methodologies, hydraulic arrangements and fabrications in order to safely construct the damper arrangement.
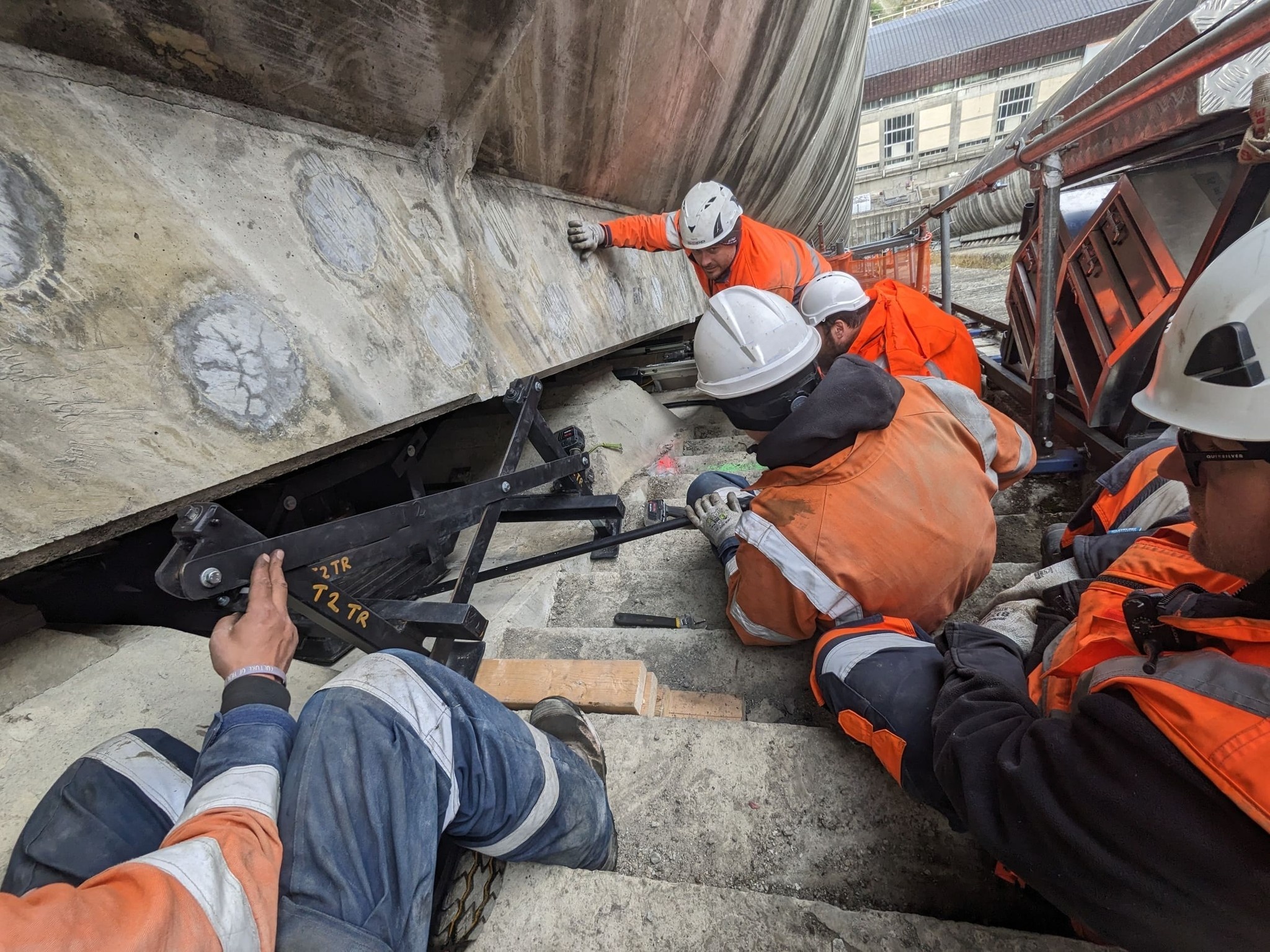
Redesigning anchor blocks for precision outcome
In addition, Seipp was critical to the design development of the anchor blocks, which in total consist of some 2300 cubic metres of reinforced concrete. We engaged a specialist supplier to develop a bespoke formwork design that would fit the unique geometry and angles within the permanent works. As a refinement, 3D modelling was used to identify clashes in reinforcement and facilitate the methodology for construction. We added value for the client by reaching out to multiple suppliers to find a cost-effective solution.
Throughout the three-part project, we were able to co-design working methodologies that were not only fit for their unique purpose, but also led to completing the scope of works over a shorter time frame and save client costs, at no compromise to efficacy.
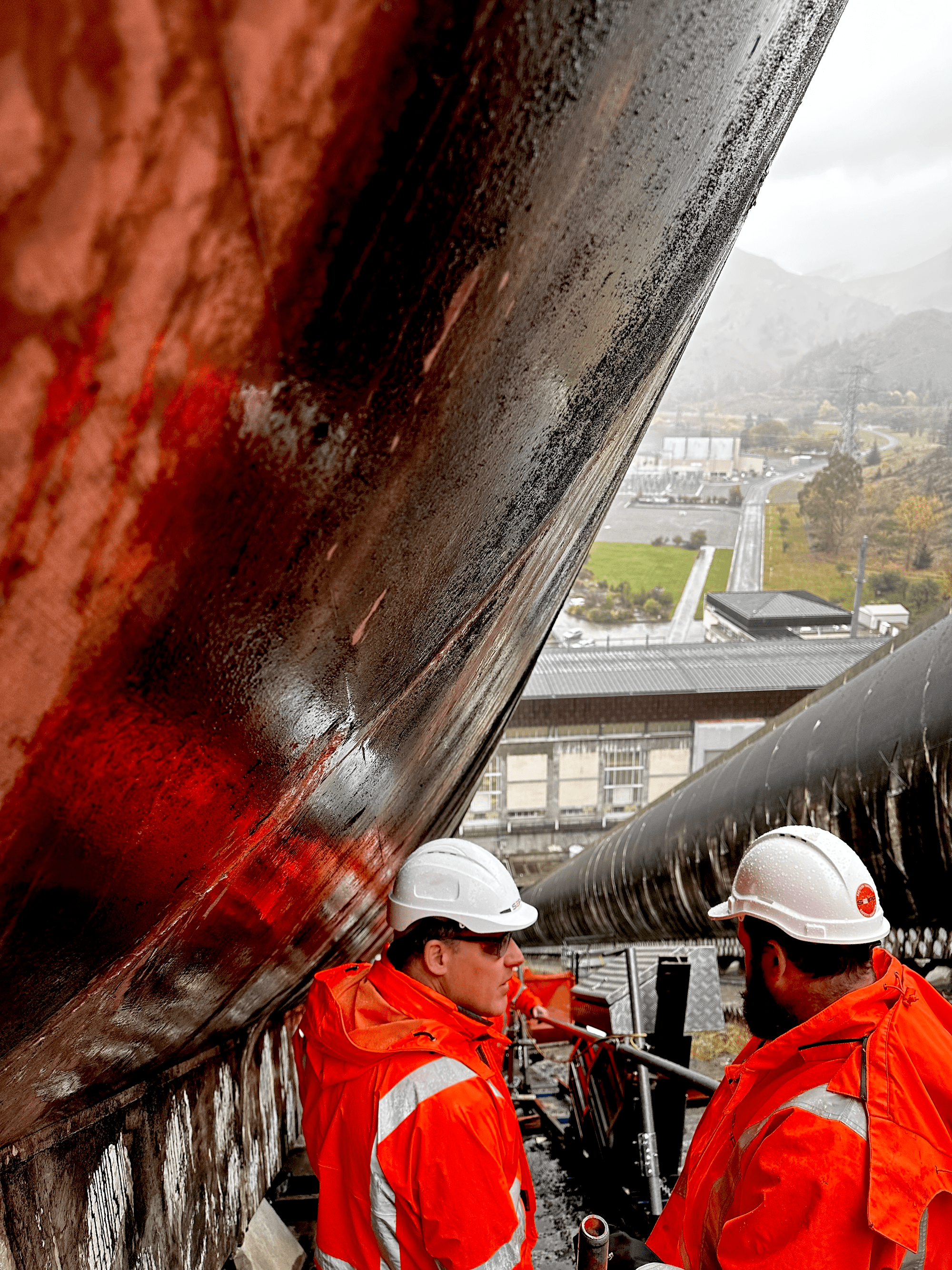
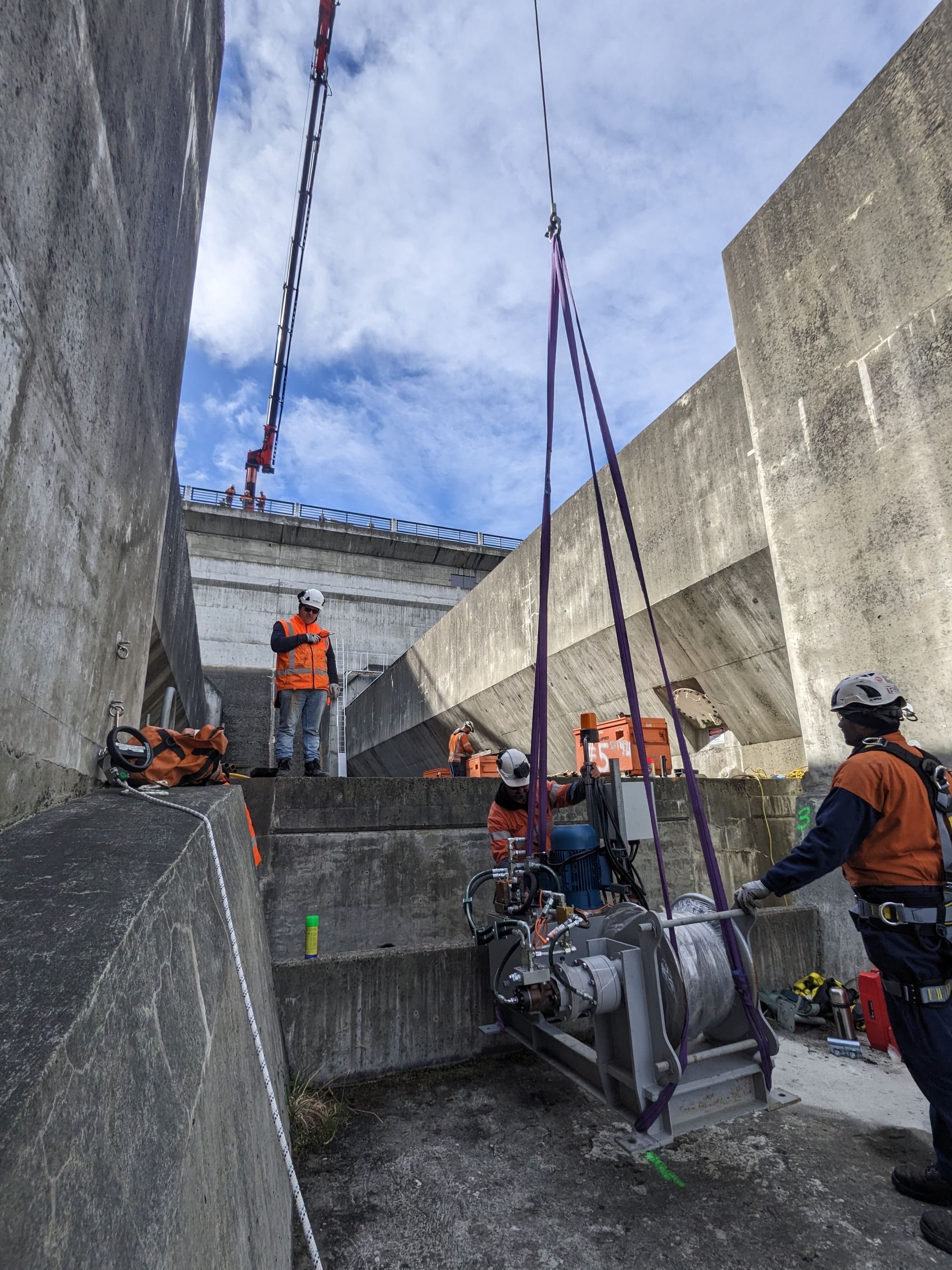
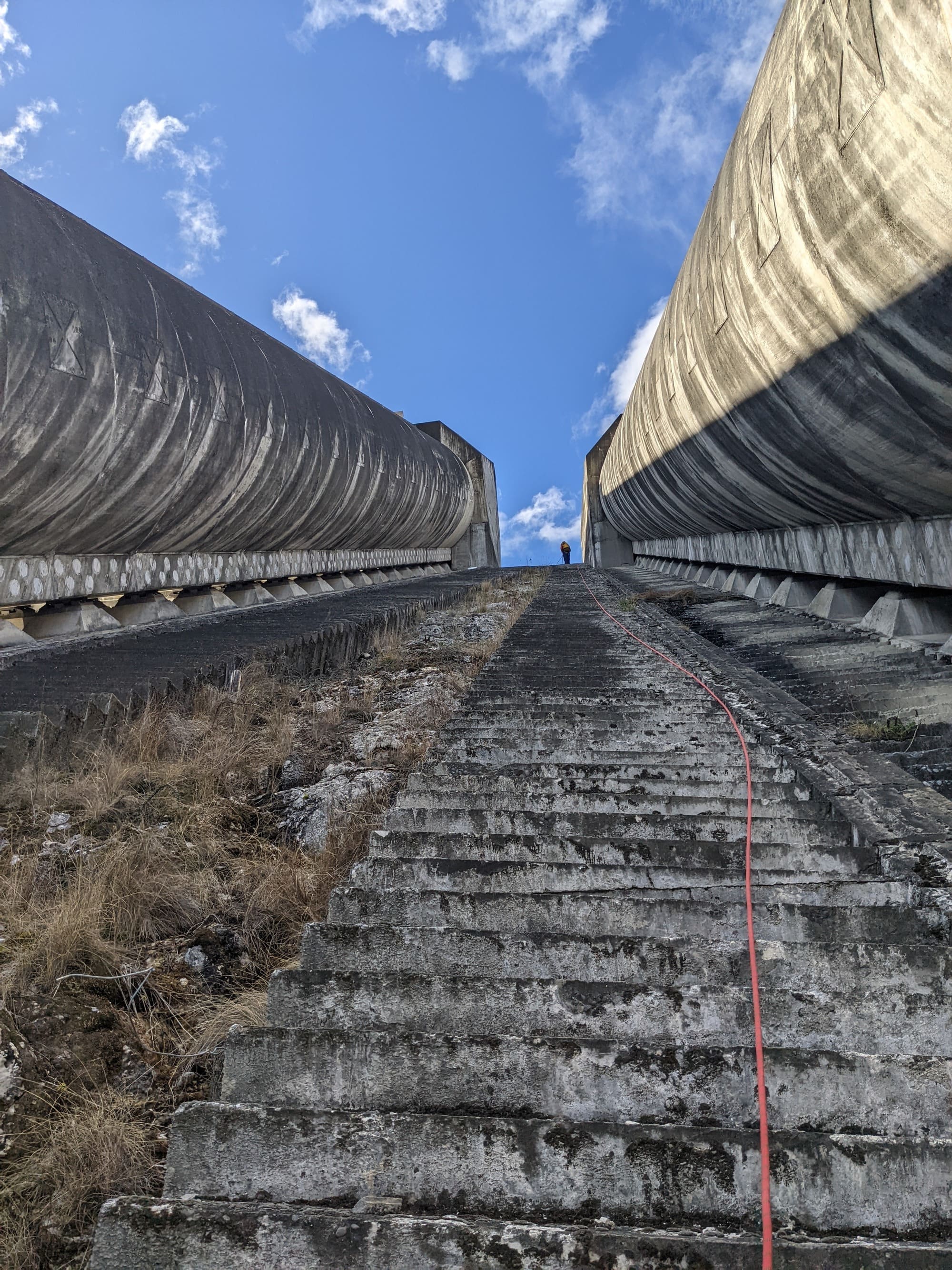
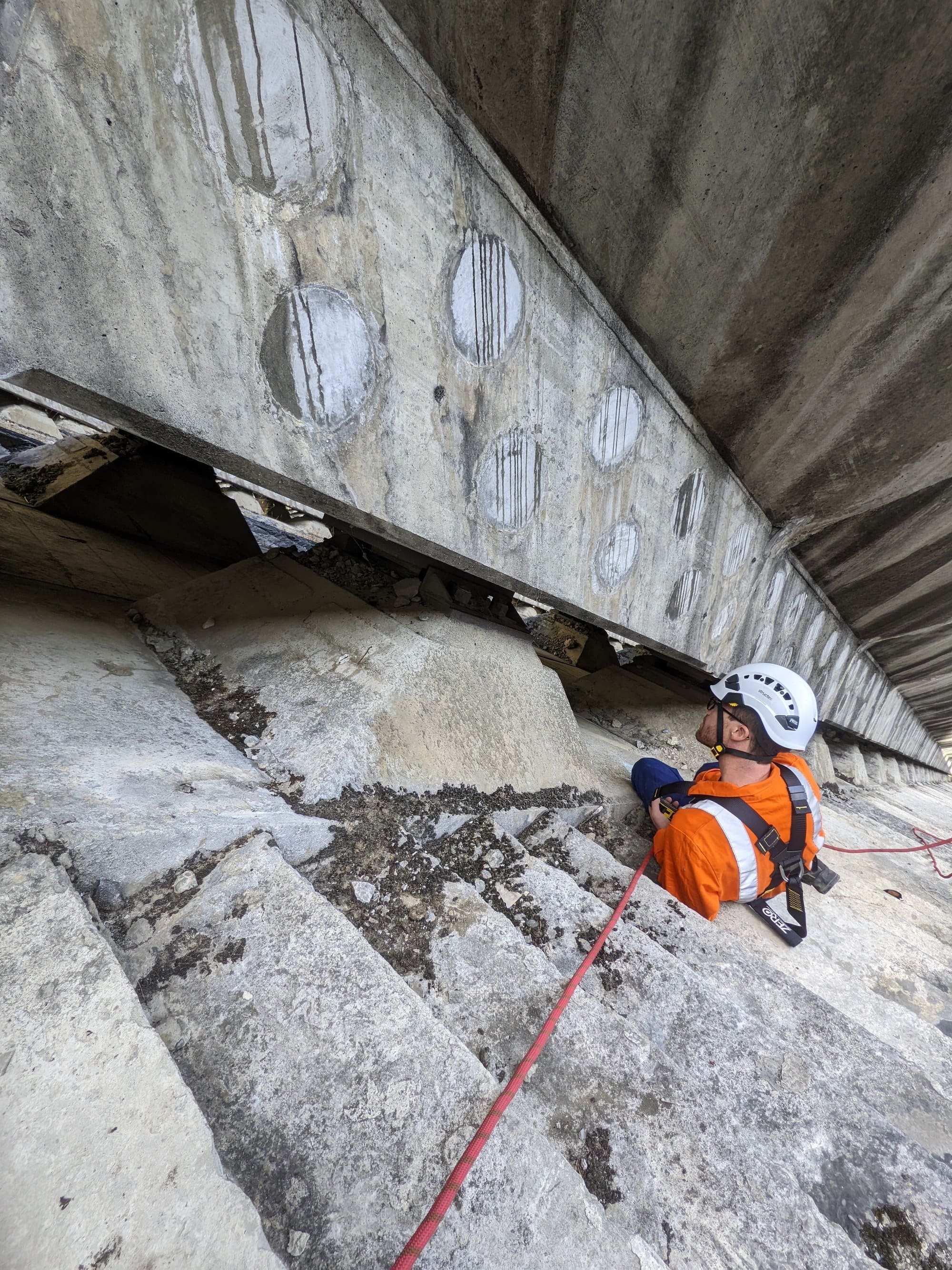
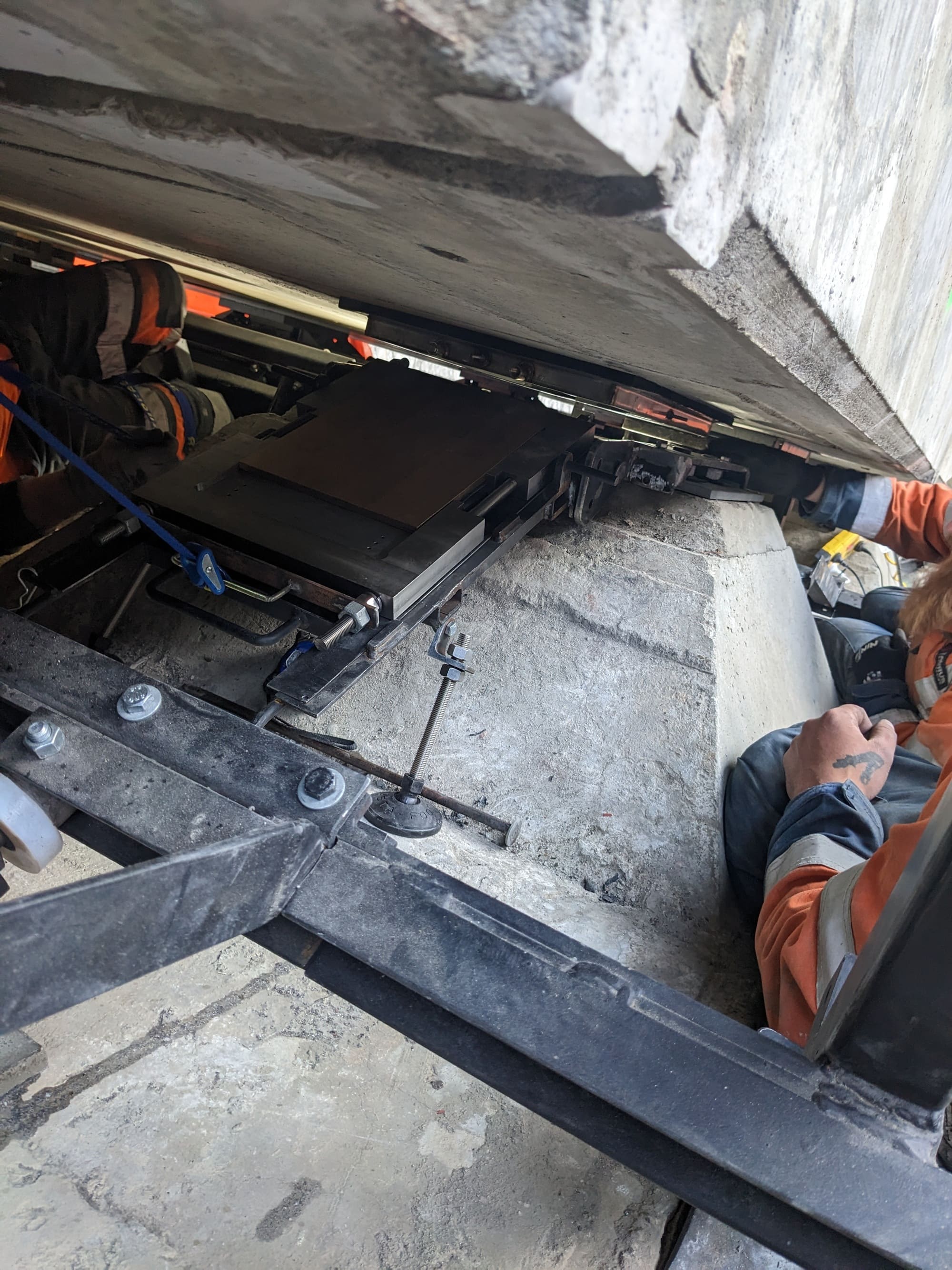